April 12, 2023
Case Study: Custom Shipping Container Compressed Air System
SHARE THIS POST
Custom Shipping Container Compressed Air System
- The customer’s primary air compressor, a competitorโs brand 75 HP variable speed compressor, was no longer able to support their production demands while operating at full capacity.
- Because of this, they were temporarily running a 100 HP rental air compressor with the 75 HP unit as a backup.
- C.H. Reed data-logged the rental compressor and recorded the facilityโs current air requirement at 227 CFM with the air compressor operating at 66% capacity.
- With reliability and efficiency being two drivers for this customer, along with the ability to scale in the future, we recommended 2 Quincy Compressor QGV-100 Rotary Screw Compressors. This way, they had a unit for back up and could alternate run times between the two.
- The system would also include a Quincy QPNC-530 Refrigerated Air Dryer, proper filtration, and a condensate separator sized to accommodate one air compressor.
- One issue the customer had before starting this project was room for the new compressors. We proposed a quick and easy solution to install the new compressors in a custom, modular shipping/storage container. Not only would this save internal real estate for them, but it provides a sheltered environment for the equipment, protecting from any dust, dirt, oil, and moisture from the production process.
- The custom modular setup would include two 20โ standard height shipping containers constructed into one enclosure, two sets of barn-style access doors for easy maintenance, and all the necessary gravity dampers, exhaust fans, led lighting, electrical outlets, plugs for thermostatically controlled heaters, and ductwork.
- Transair Compressed Air Piping was installed, interconnecting the new equipment to their existing air receiver right inside the building.
- Along with Quincy Compressorโs industry leading 10-year airend warranty for the QGV compressors, we setup Quincy ICONS monitoring system, giving them the ability to receive monthly service emails, machine service status, online performance dashboards, and service logging.
Project Photos
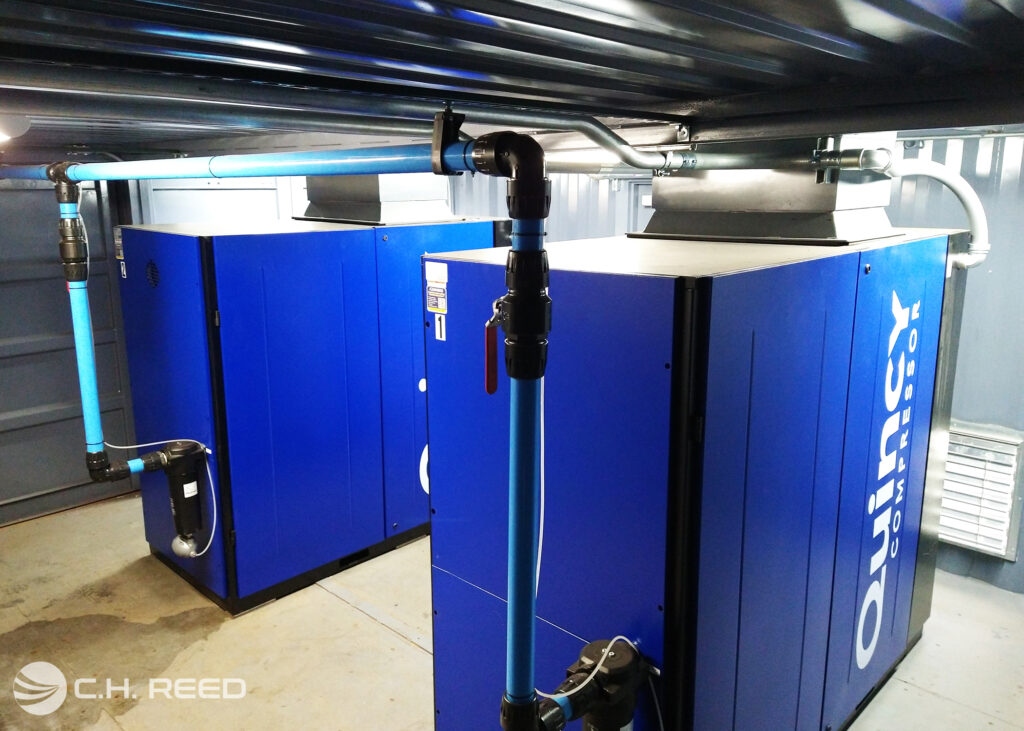
Finished photo of the Quincy QGV-100 Compressors inside the shipping containers
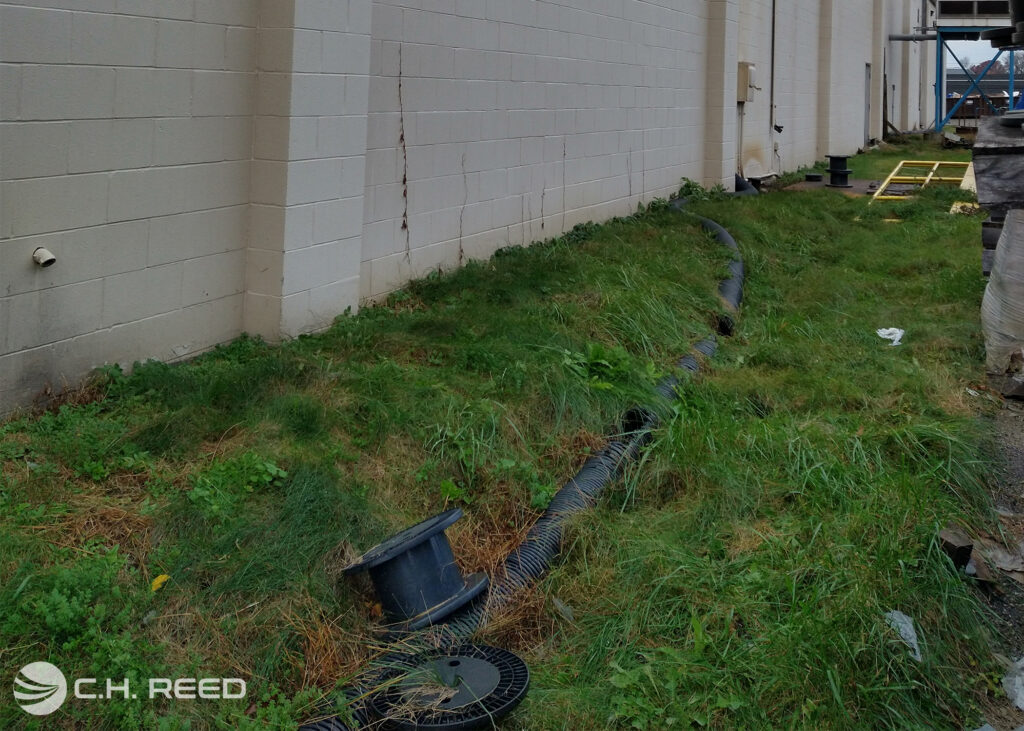
Before photo of the project’s location
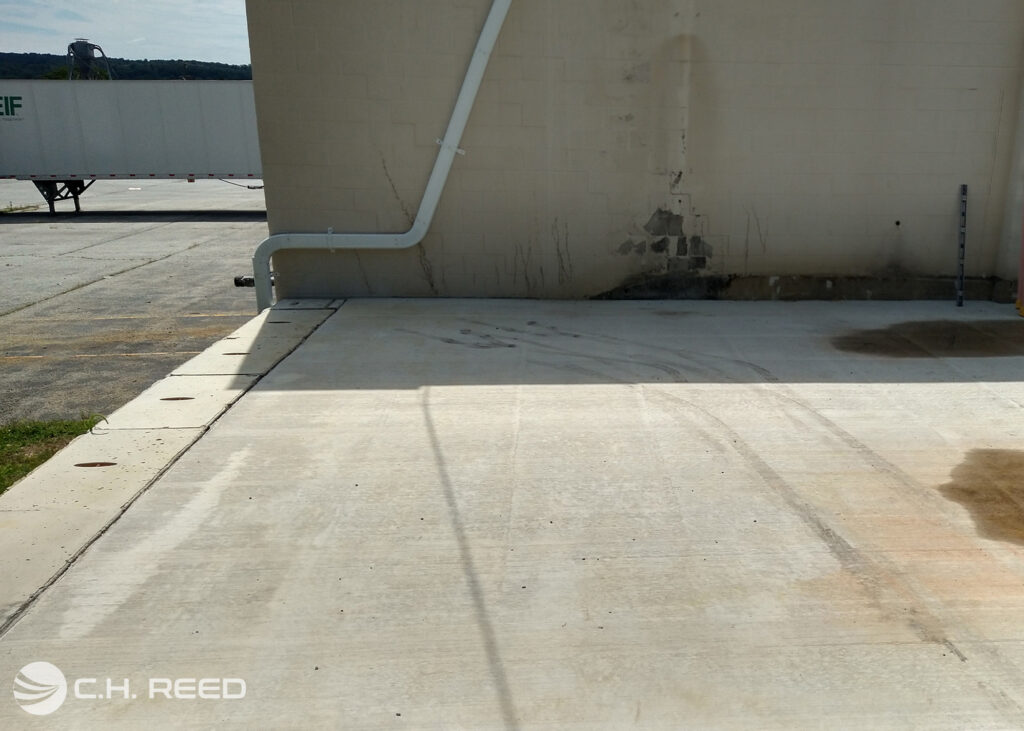
A concrete pad gets poured for the containers
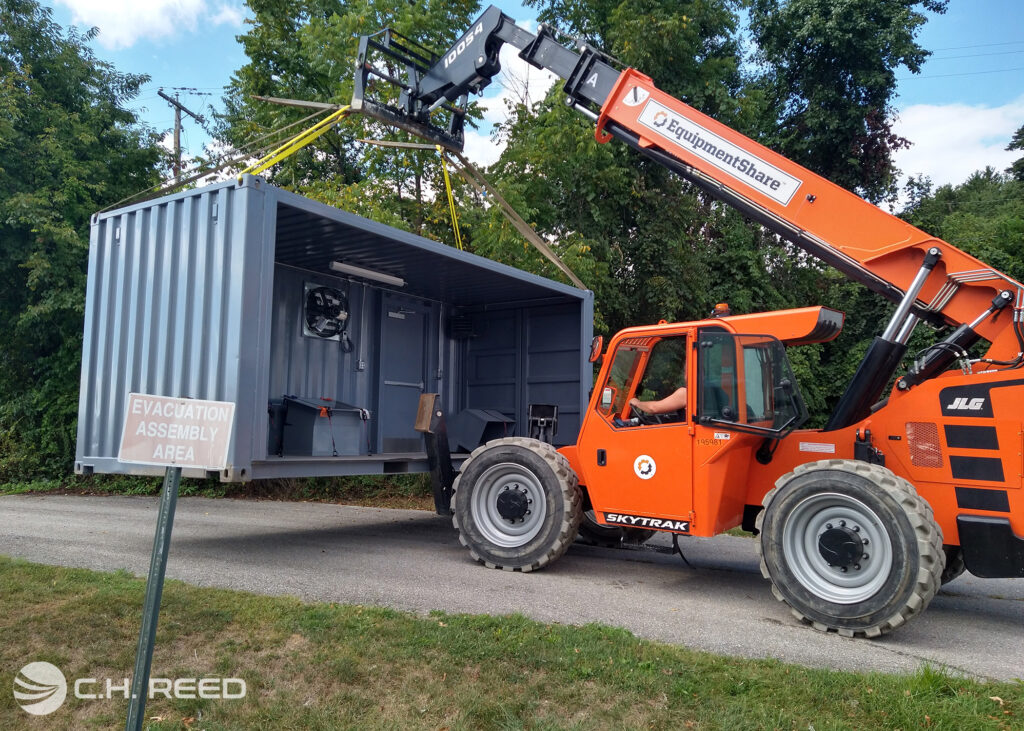
Two shipping containers are hauled in and placed on the concrete pad
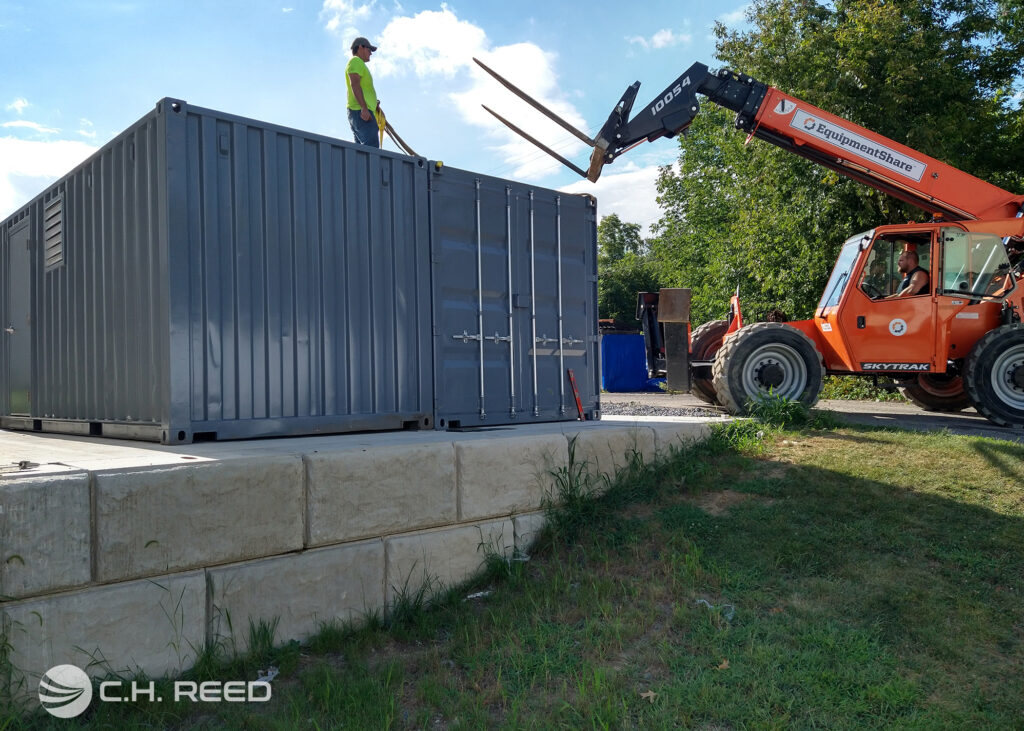
The two shipping containers are placed on the concrete pad and fabricated together to form one enclosure
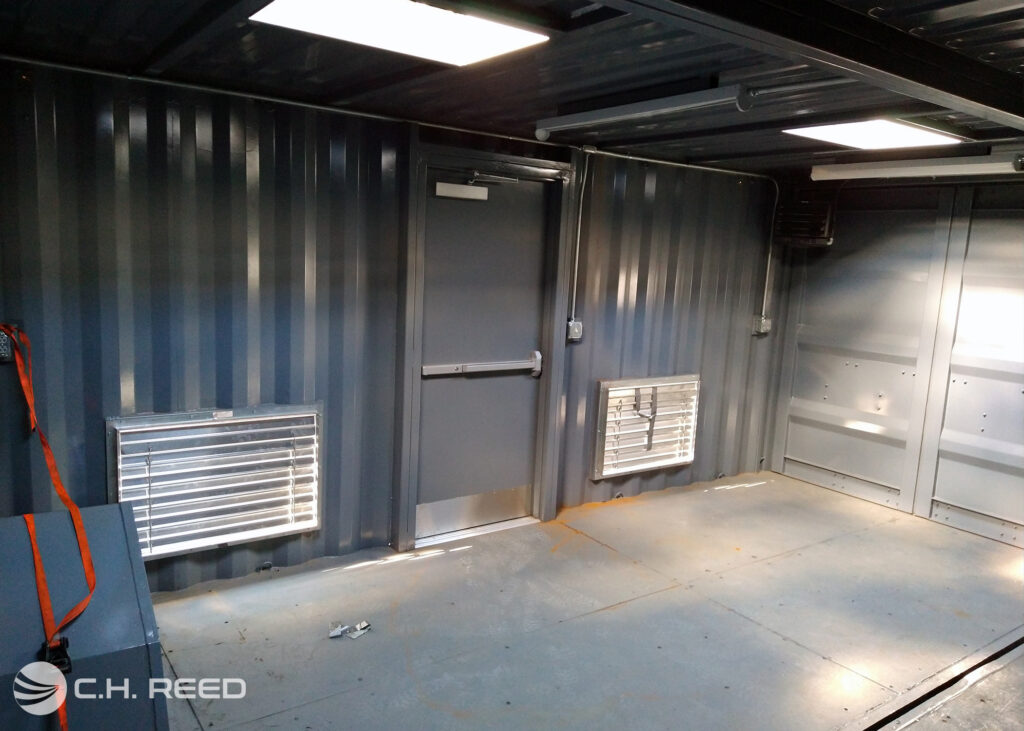
A look inside the two containers before the compressors are installed
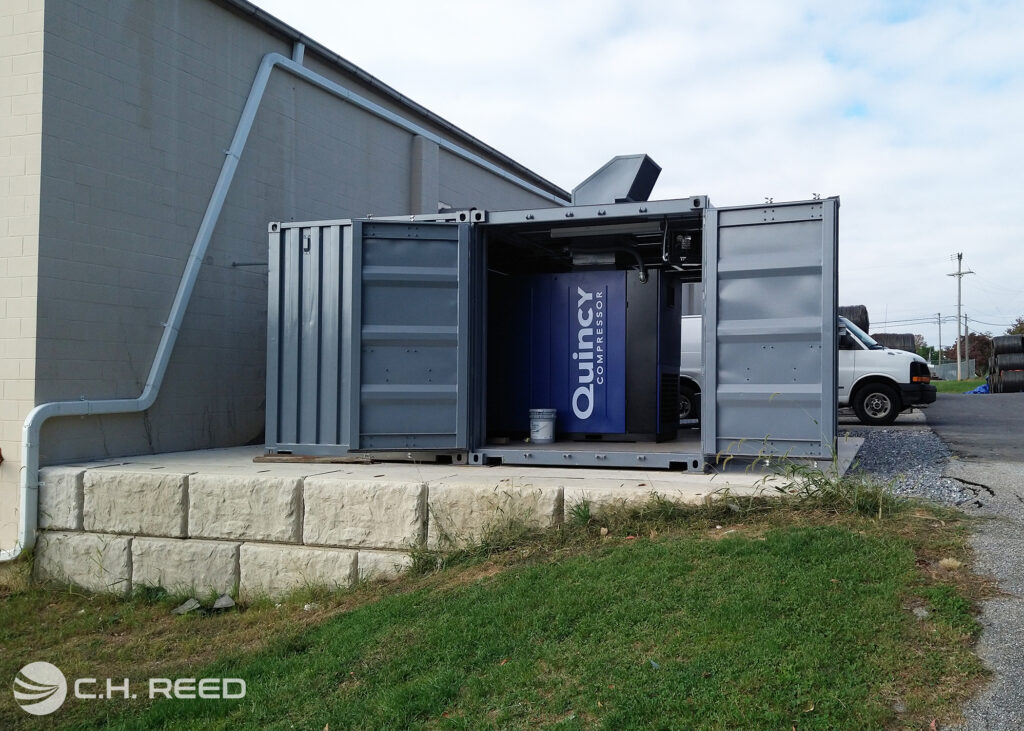
Both QGV-100 air compressors are installed in the enclosure
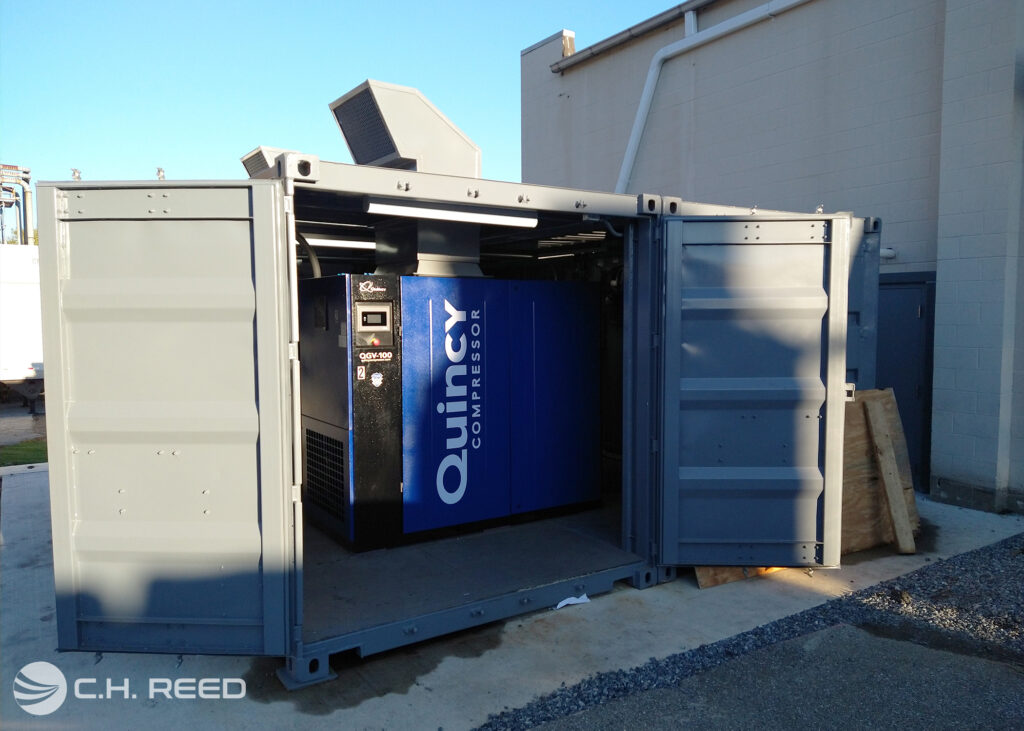
Barn style doors make for easy access for maintenance
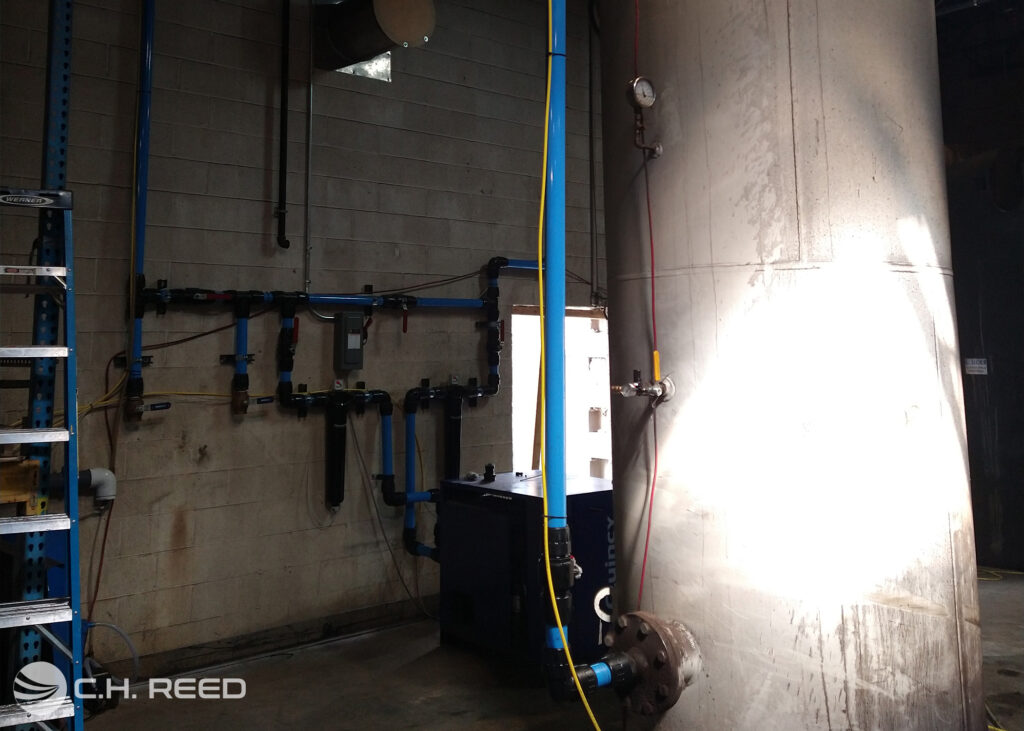
A new Quincy air dryer and existing air storage take are installed, along with filtration, right inside the building
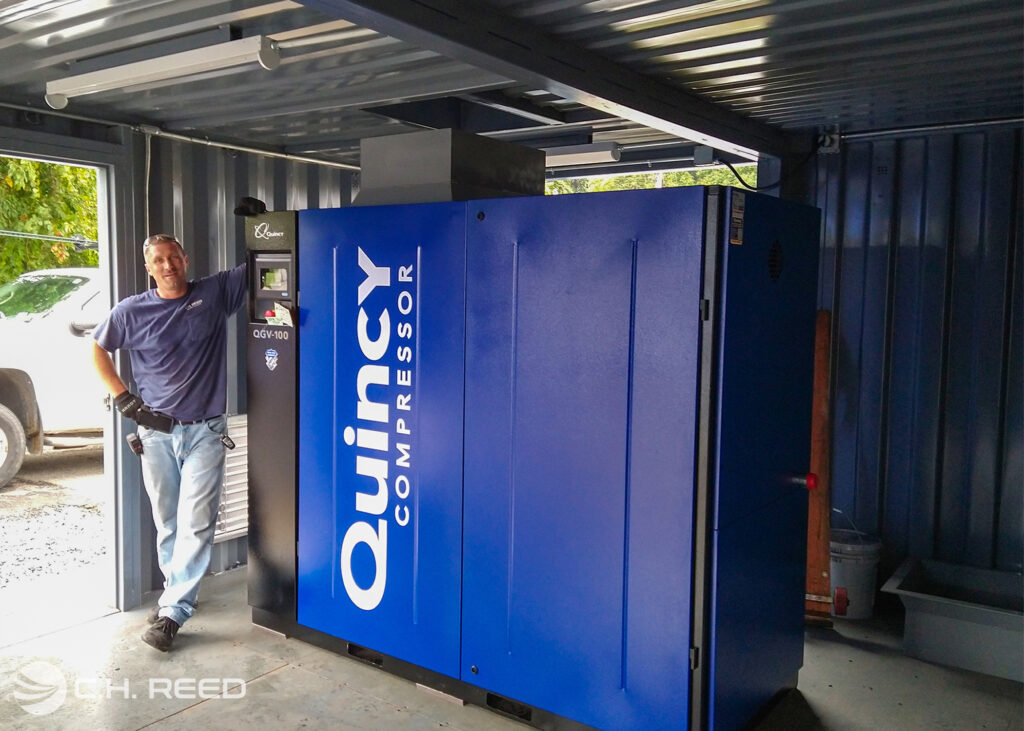
Caleb Maus, our Compressed Air System Specialist who headed up the job
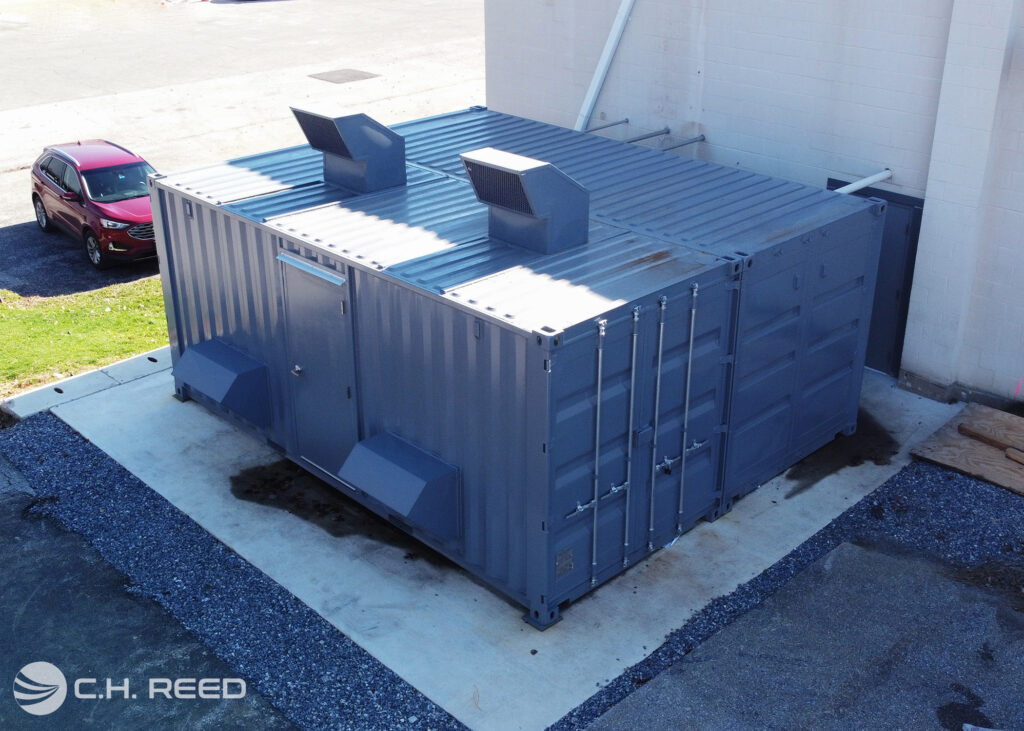
An overhead shot of the finished, custom shipping container compressed air system
Search
Categories
Get a consultation
Related Posts
The 3 Distinct Advantages of Hydraulic Powered Pumps
Recently, C. H. Reed helped a major printing operation install a new ink pumping system. Theย newย system needed to transfer four colors of highย viscosity, heat-set ink to their three presses, drawing the ink from multiple 5,000…
Simple Ways to Reduce Waste in Your Spray Finishing System
In todayโs demanding manufacturing landscape, it can be convenient to adopt a โcut-costs-at-all-costsโ mentality, justifying questionable means for the sake of leaner production, a lower bottom line and increased profitability.ย Regrettably, those efforts can interfere…
What You Need to Know About Air-Powered Pressure Washers
Pressure washers are great solutions for your average cleaning applications, but what tool do you turn to for your more challenging applications?ย There are many instances where it is simply impossible to use a traditional…