July 31, 2017
Diaphragm Pumps: AODD Pump Basics
SHARE THIS POST
How Does a Diaphragm Pump Work
Diaphragm pumps are a series of pumps that fall under the positive displacement family of pumps. Air-operated double diaphragm pumps (AODDs) have a simple design in which two diaphragms are attached to a common connecting rod. The pump is driven by compressed air through an air distribution system which reciprocates the diaphragms. As one pumping chamber is displaced, the other chamber loads. The process then repeats as the pump changes direction. Inlet and outlet checks either seat or unseat in the process. See video demonstration below.
Advantages of AODD Pumps
Seal-less Design: The pumping chamber and fluids are not in contact with any close fitting seals. This makes them ideal for abrasive applications such as slurries or highly filled materials, as well as shear sensitive materials like UV coatings. Leakage issues associated with close fitting rotary or sliding seals on other pump designs are eliminated as well. Another advantage of the seal-less design is that they can run dry without damage; which is not the case with many other types of pumps with close fitting seals.
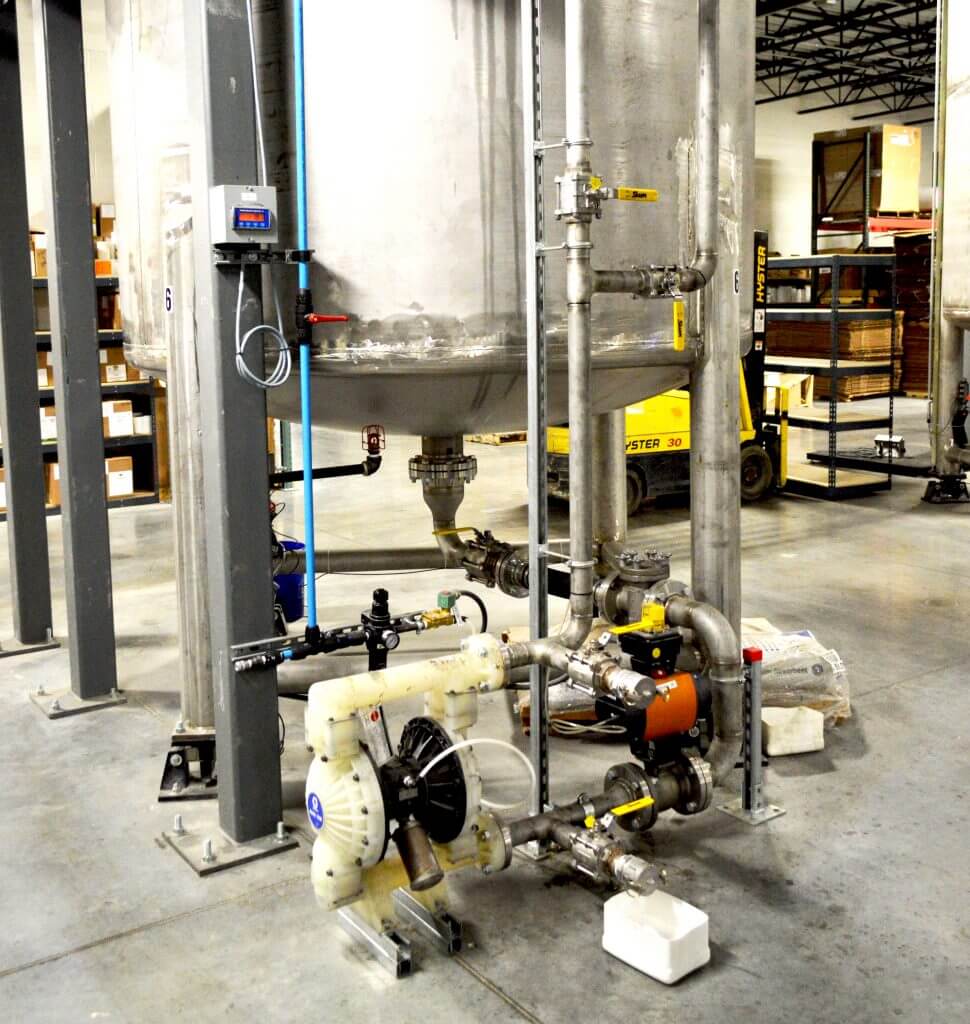
2″ AODDs used in transfer of liquid fertilizer from bulk tanks to packaging machines. Customer previously used gear pumps but had issues with leaking; creating an unsafe work area and high maintenance costs.
Chemical Compatibility: A wide range of wetted parts and elastomers are available to handle most any fluid, solvent, or chemical.
Air Driven: Being air driven, these pumps (in the right configuration) are intrinsically safe for use in hazardous locations like transferring solvents from storage areas. They will stall under pressure if deadheaded; eliminating the need for safety devices to shut down electric driven pumps under the same conditions.
Ease of Installation: AODDs are relatively easy to install and can be made into portable configurations for increased flexibility.
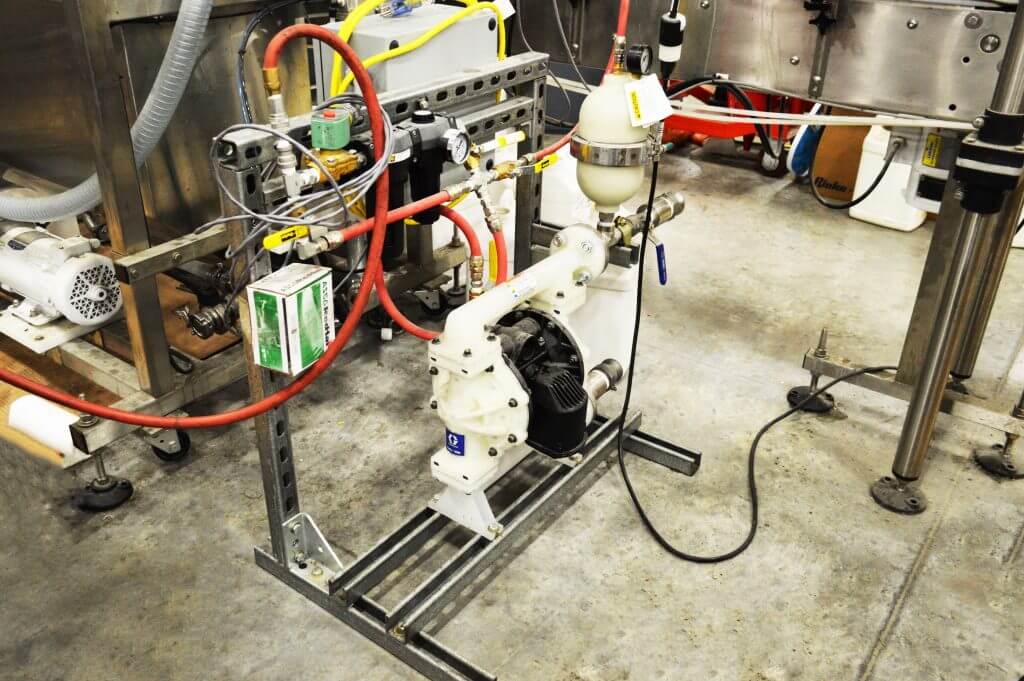
Portable AODD skid with automatic on/off sensor for filling packaging line tanks from 300 gallon totes on short run line.
Self-Priming: Diaphragm pumps are self-priming and do not require flooded suction.
Solids Handling Capacity: Porting and check design allows for handling of materials with high solids content. A 3” ball check diaphragm pump can pass solids up to .5”. Flap valve check designs are available that pass solids 2.5”and greater.
Abrasion Resistance: As noted earlier, the seal-less design (coupled with large internal porting) allows for handling of very abrasive materials. High performance elastomers and diaphragm designs have been developed to enhance this feature.
Ease of Control: Being air operated, AODDs’ capacities can be variable within the pumps operating range without the use of variable speed motors or VFDs. Batching can be accomplished using relatively simple cycle counters.
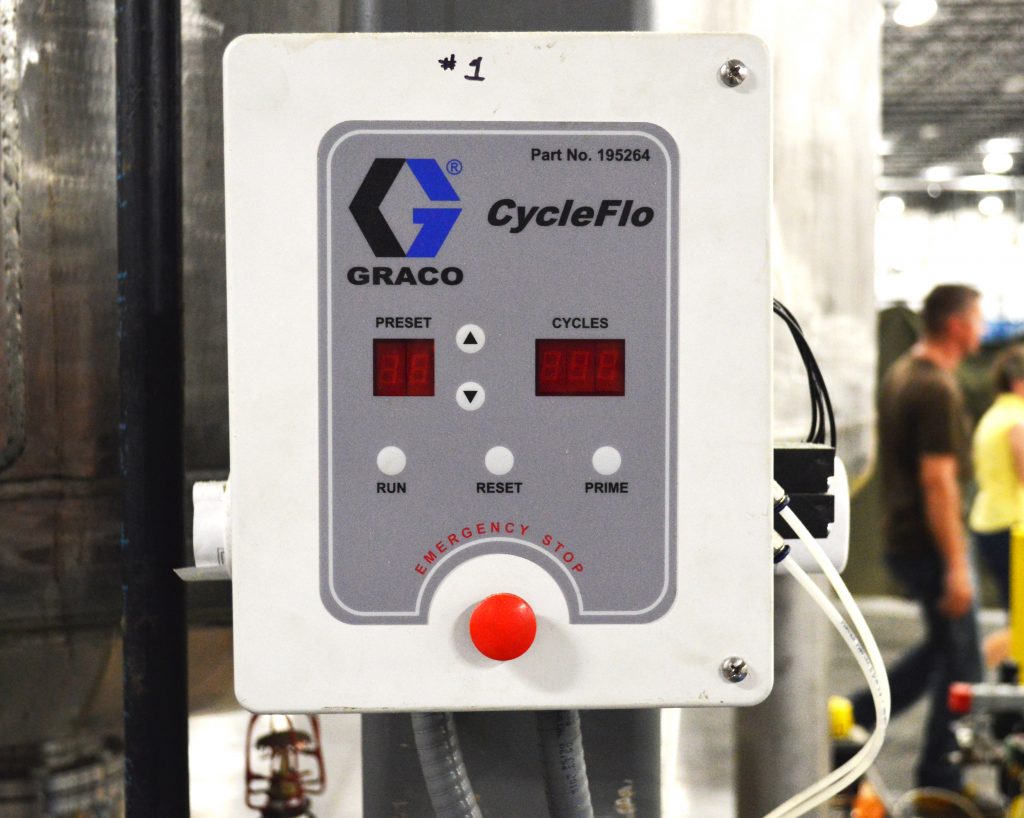
Programmable cycle counters being used for batching materials from bulk tanks to mix stations. Controllers allow for multiple recipes to be stored and automatic operation. Pump will stop and reset when desired preset number of cycles have been achieved.
Capacities & Pressure: AODDs come in a wide range of capacities; from less than 5 GPM (gallons per minute) up to roughly 300 GPM. The majority are 1:1 ratio pumps, meaning for every one PSI of air pressure, the pump will generate one PSI fluid pressure. There are also some 2:1 and 3:1 ratio AODDs available that generate higher pressures for applications like filter press feed.
Limitations of AODDs
Flow & Pressure: As mentioned above, flow & pressures for AODDs max out at about 300 GPM. For applications that require flow rates above 300 GPM, you can use piston pumps, gear pumps, or centrifugal pumps. (Random fact: The U.S. Army Corps of Engineers developed a flood control system for New Orleans after 2005’s devastating Hurricane Katrina. The system includes 17 massive pumps capable of pumping 11 million GPM from the canals into nearby Lake Pontchartrain in the event of hurricane storm surges. Those are some monstrous pumps!)
Energy Efficiency: AODDs costs roughly 4-5 times what an electric driven pump costs to run. Based on your number of pumps and flow rates, this should always be weighed when evaluating the best technology for your application. Newer generation electric-driven double diaphragm pumps are available offering all the advantages of AODDs with the energy efficiency of an electric driven motor.
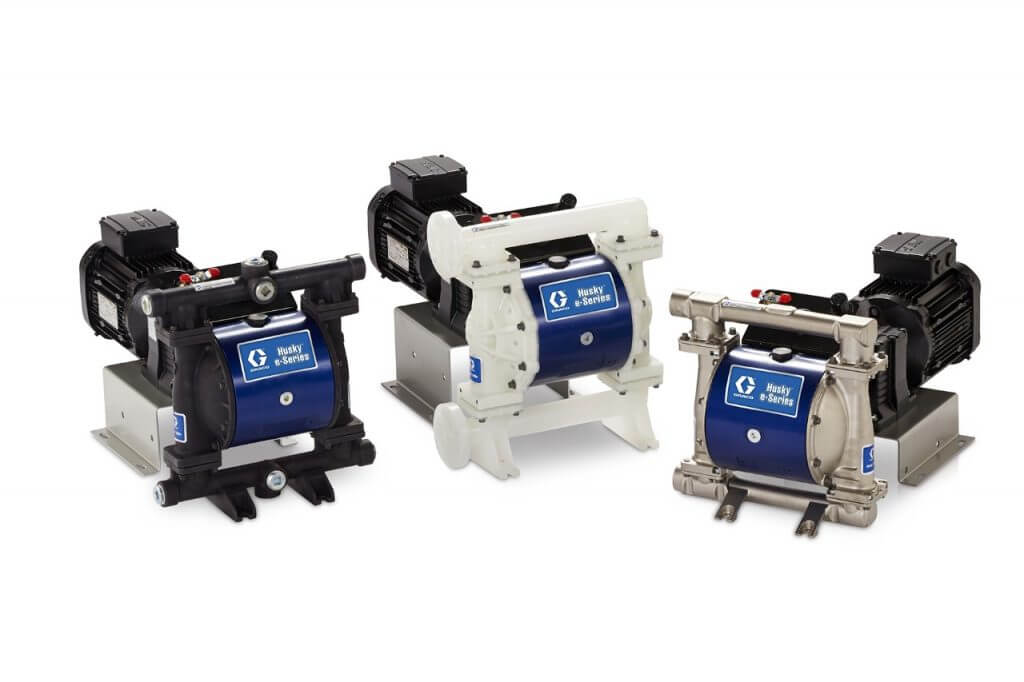
Graco Electric Diaphragm Pumps have all the benefits of air operated diaphragm pumps and then some. Contact us to learn more!
Pulsation: AODDs generate a pulse or surge when they shift directions. This pulse can be greatly reduced with the use of surge suppressors. Newer electric-driven pumps can overcome this condition as well.
Stalling: Under certain conditions such as high back pressure or trying to operate the pump at its lower operating range, the pumps can stall or “center”. Always review the pump’s air valve design and operating conditions with your supplier before choosing.
If you have a fluid transfer application and would like to learn about air operated double diaphragm pumps, electric diaphragm pumps, or any other pump specific to your application, contact C.H. Reed today to speak with a process specialist.
Search
Categories
Get a consultation
Related Posts
The 3 Distinct Advantages of Hydraulic Powered Pumps
Recently, C. H. Reed helped a major printing operation install a new ink pumping system. The new system needed to transfer four colors of high viscosity, heat-set ink to their three presses, drawing the ink from multiple 5,000…
Simple Ways to Reduce Waste in Your Spray Finishing System
In today’s demanding manufacturing landscape, it can be convenient to adopt a “cut-costs-at-all-costs” mentality, justifying questionable means for the sake of leaner production, a lower bottom line and increased profitability. Regrettably, those efforts can interfere…
What You Need to Know About Air-Powered Pressure Washers
Pressure washers are great solutions for your average cleaning applications, but what tool do you turn to for your more challenging applications? There are many instances where it is simply impossible to use a traditional…